Below is a technical overview for our wet pour rubber safety surface. Please Visit our Wet Pour Rubber product page for more information.
Wet Pour – Composition
Wet pour rubber safety surfacing is a flexible two-course system which can be installed to varying depths. The non-slip top layer, known as the wearing course, consists of tough and durable EPDM rubber granules mixed with a polyurethane binder. These clean cut and clean faced granules provide a well bonded surface with a high tensile strength that will prove to be extremely durable.
Black surfaces use a recycled EPDM rubber derived from the waste produced in the manufacture of industrial rubber mouldings and also from rubber seals derived from the automotive trade. Coloured surfaces are formed from virgin EPDM rubber and are coloured throughout.
The base course comprises granulated recycled rubber and polyurethane binder to varying depths dependent on the play equipment above. The soft base layer cushions the fall, progressively deforming and lengthening the impact over time and distance.
Wet pour rubber can be used to overlay an existing wet pour surface in most circumstances. In these situations it is imperative that the substrate is completely dry before being overlaid. If dampness is present it is possible that the overlaid material will not adhere to the existing surface.
Sub Base Specification When Depth is 40mm or Greater
When being installed into a natural grass area we prefer not to use edgings where at all possible. A more natural look is achieved in this way. The wet pour is instead buried below the grass. In addition, not using edgings means that the installation is less costly. Finally, also remember that not using edgings means less resources are being used to complete the installation, so it is a more sustainable approach.
We look to raise the new surface very slightly above the surrounding grass in order to aid drainage.
The depth of sub base required will vary according to the ground conditions. We recommend that the sub base should be a minimum of 50mm compacted depth, and that it should be laid onto a geotextile membrane. It may be that ground conditions dictate the depth of sub base could be greater than 50mm.
If a perimeter edge detail is required (for example, the wet pour might be butting up to other surfaces as part of a larger landscape scheme) we recommend that a concrete, brick or steel edge is used. See the following drawing.
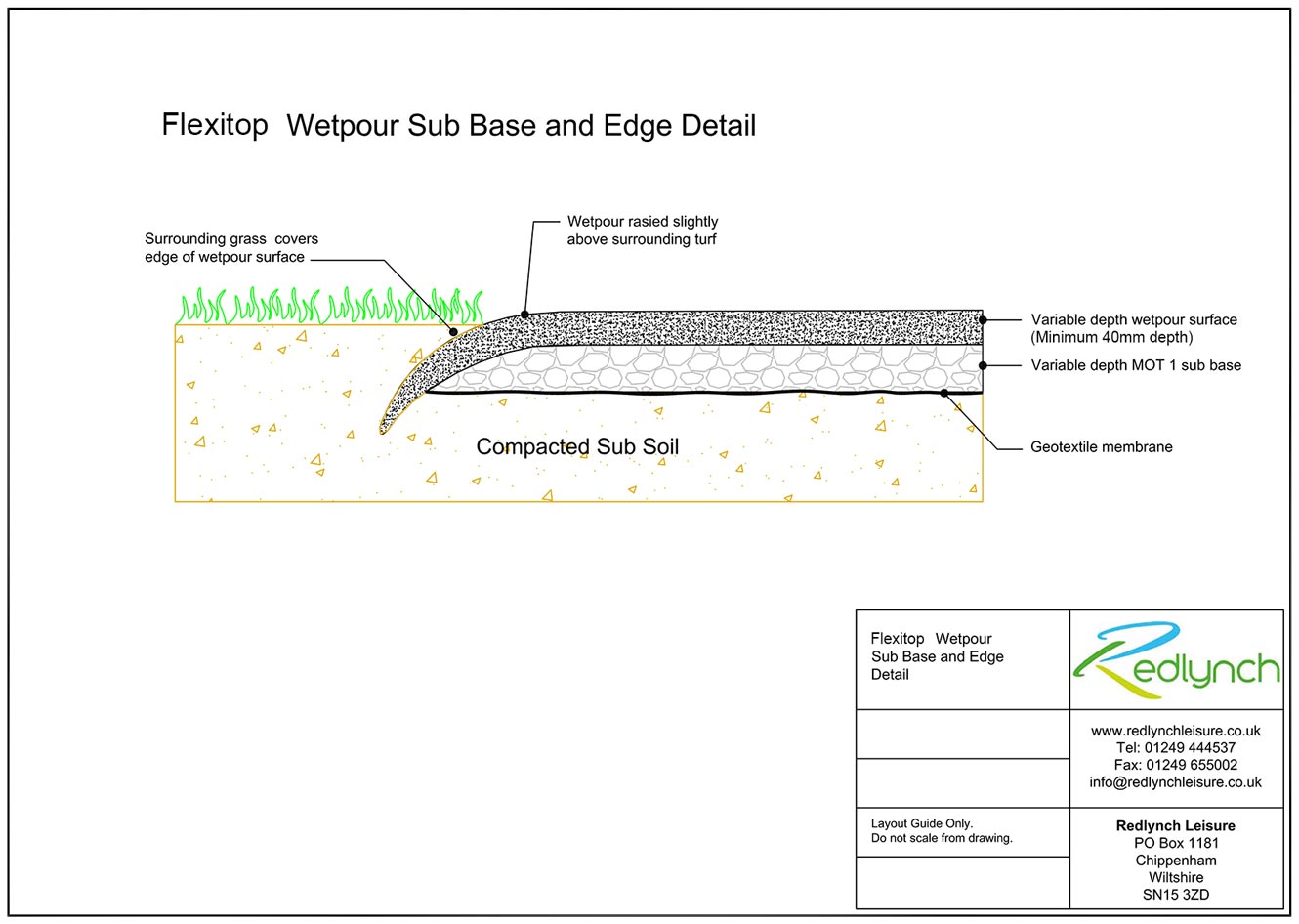
If a perimeter edge detail is required, we recommend that a concrete, brick or steel edge is used. See the following drawing
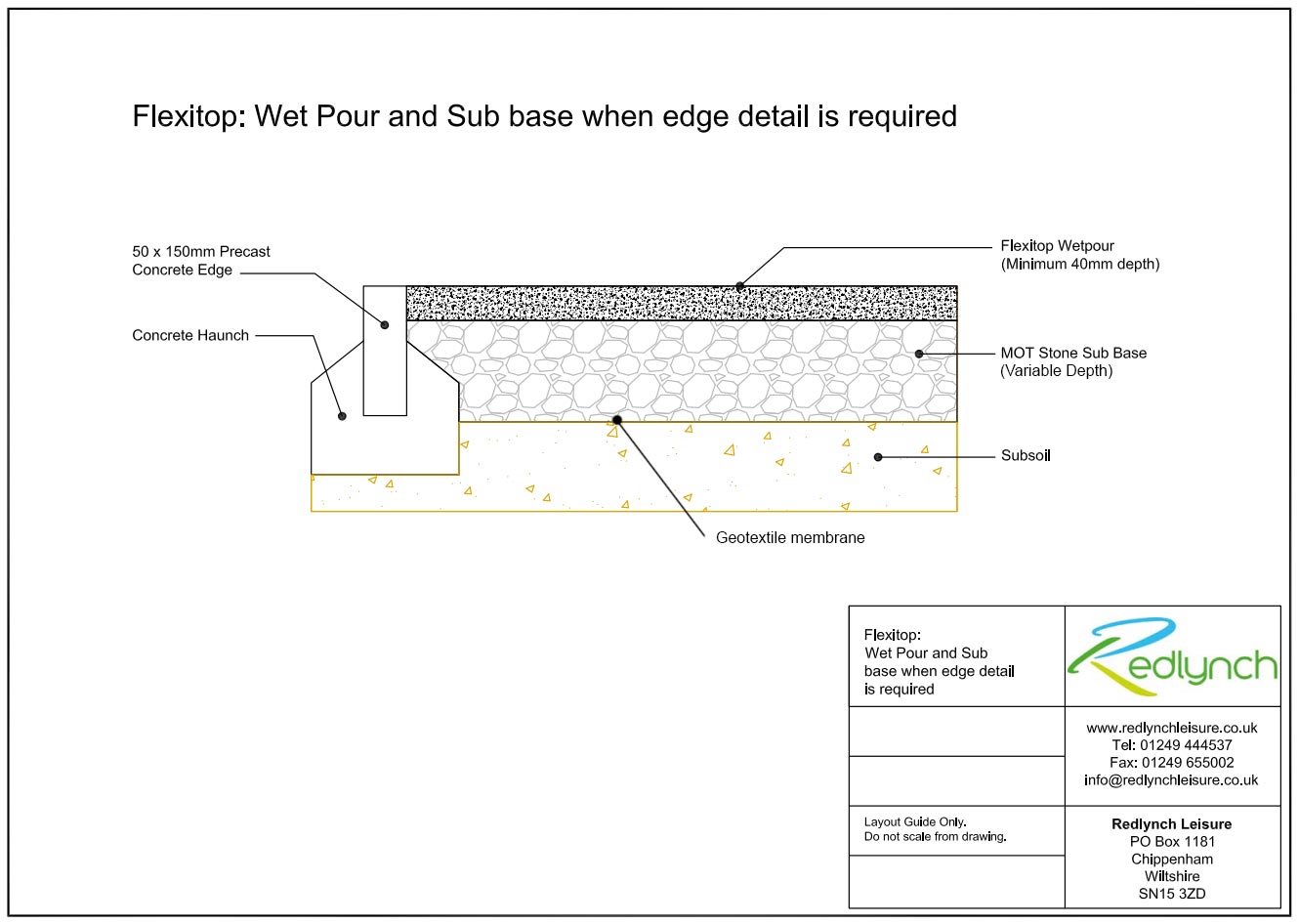
We would no longer recommend timber edging to provide a perimeter detail for wet pour safety surface. Modern timber treatment methods mean that when timber is in direct contact with the ground is not able to withstand rot.
When the depth of wet pour is below 40mm it must be installed onto a free draining tarmac or concrete substrate
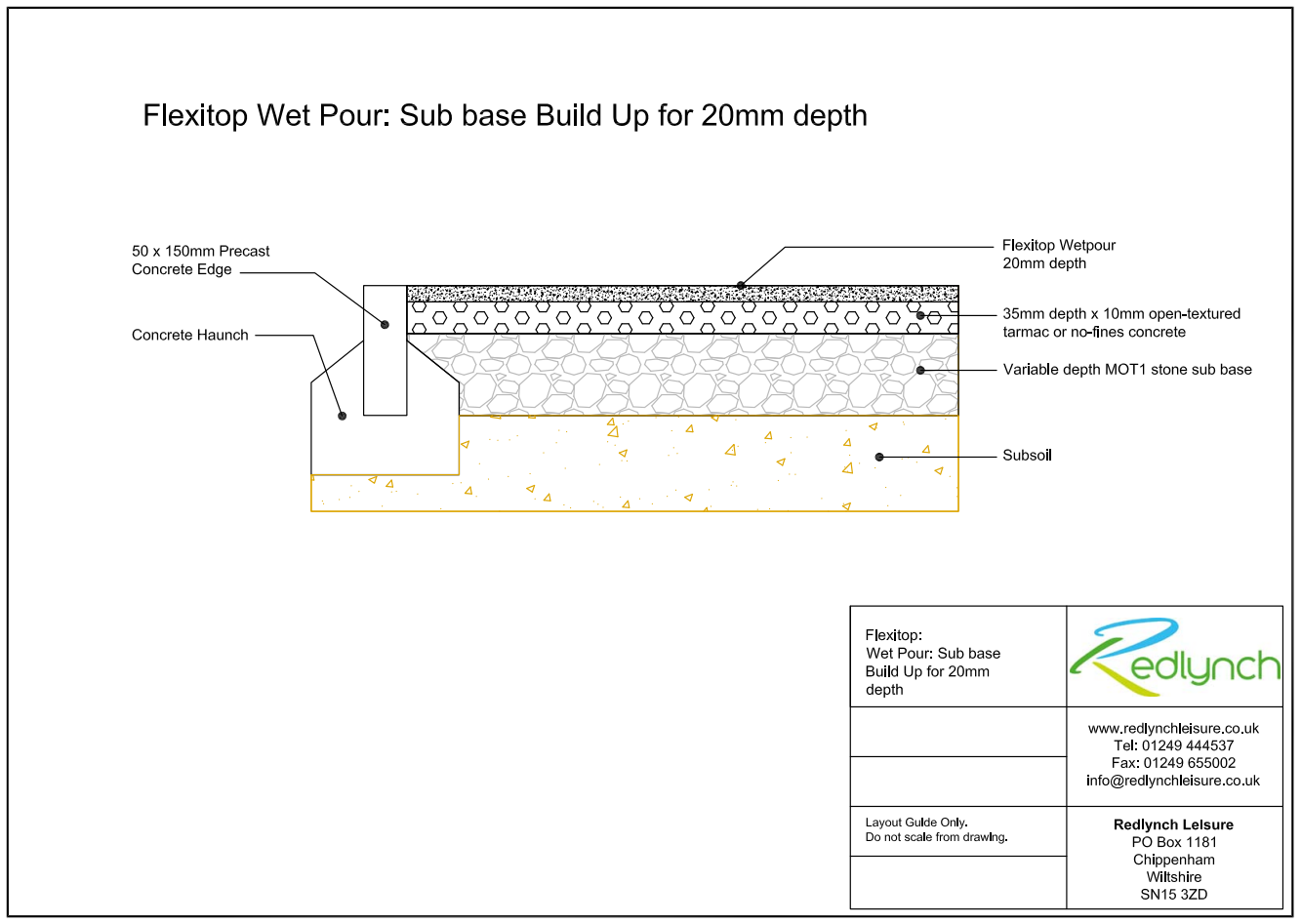
Sub base specification when laid directly onto existing concrete/tarmac
• FlexiTop wet pour rubber can be laid on top of existing concrete/tarmac in satisfactory condition by creating ramped perimeter edges.
• Cut a chase 25x25mm into concrete/tarmac at perimeter of area. Ensure that the minimum required surface area for any play equipment is at the full depth (i.e. not ramped).
• Where the surface depth is 50mm or less, the length of the ramp is to be twice the depth of surface.
• Where the surface depth is above 50mm, the length of the ramp is to be 2.5 times the depth of surface.
• If the tarmac / concrete holds water during and after rainfall it may be necessary to drill drainage holes through the tarmac to improve drainage
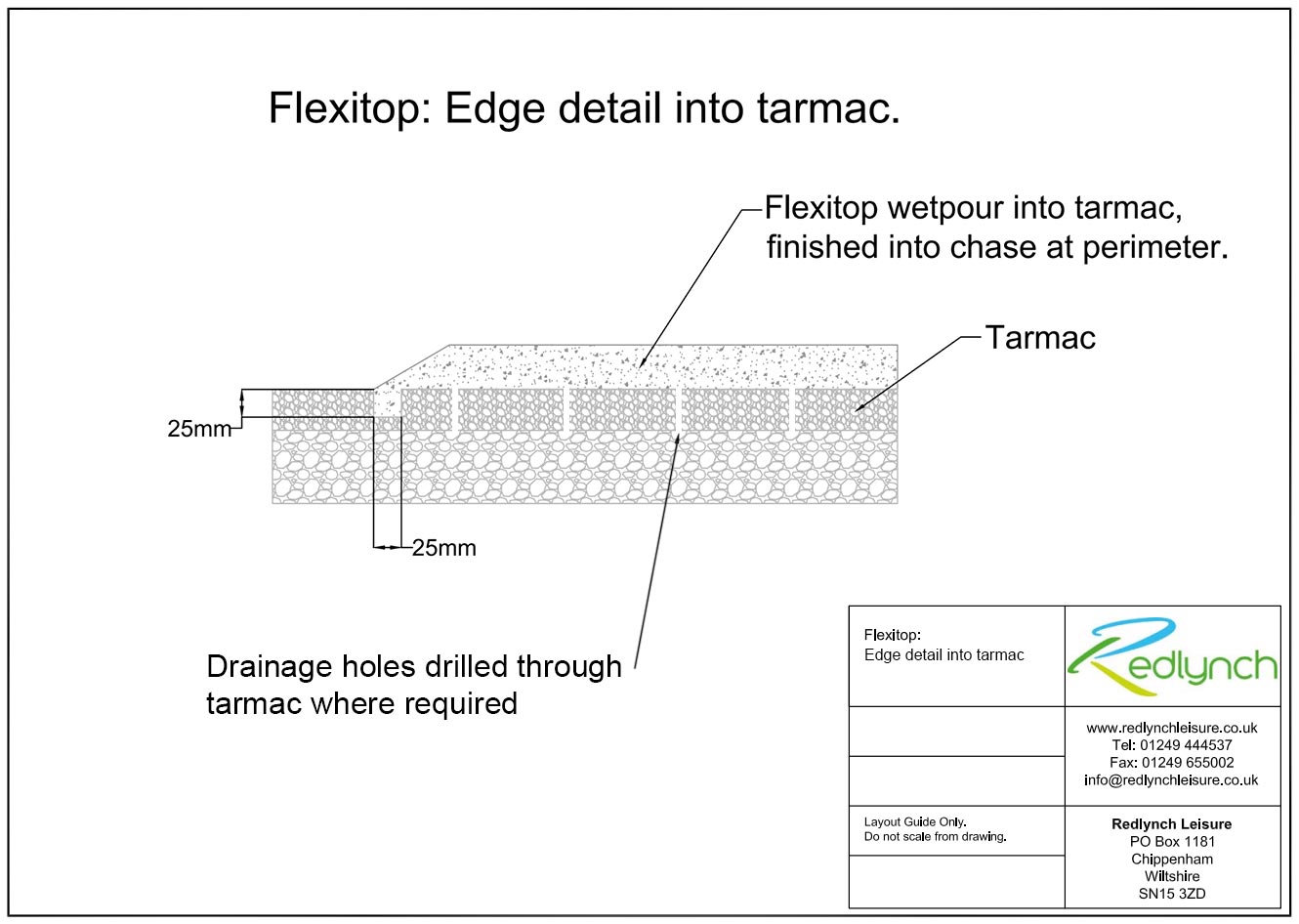
Wet Pour Rubber, Fall Height Chart
Depth of Wet Pour |
20mm
|
40mm
|
50mm
|
70mm
|
79mm
|
100mm
|
140mm
|
Free Fall Height | 0.7m | 1.3m | 1.7m | 2.3m | 2.5m | 2.8m | 3.2m |
Repairs and Maintenance
A sub base with adequate drainage is essential to ensure that water can be removed from the surface. Over time the surface may become dirty if the interstices between the granules become blocked. Occasional cleaning is highly recommended.
Should the surface become damaged, it can be repaired. We recommend this takes place as soon as possible after the damages has occurred.
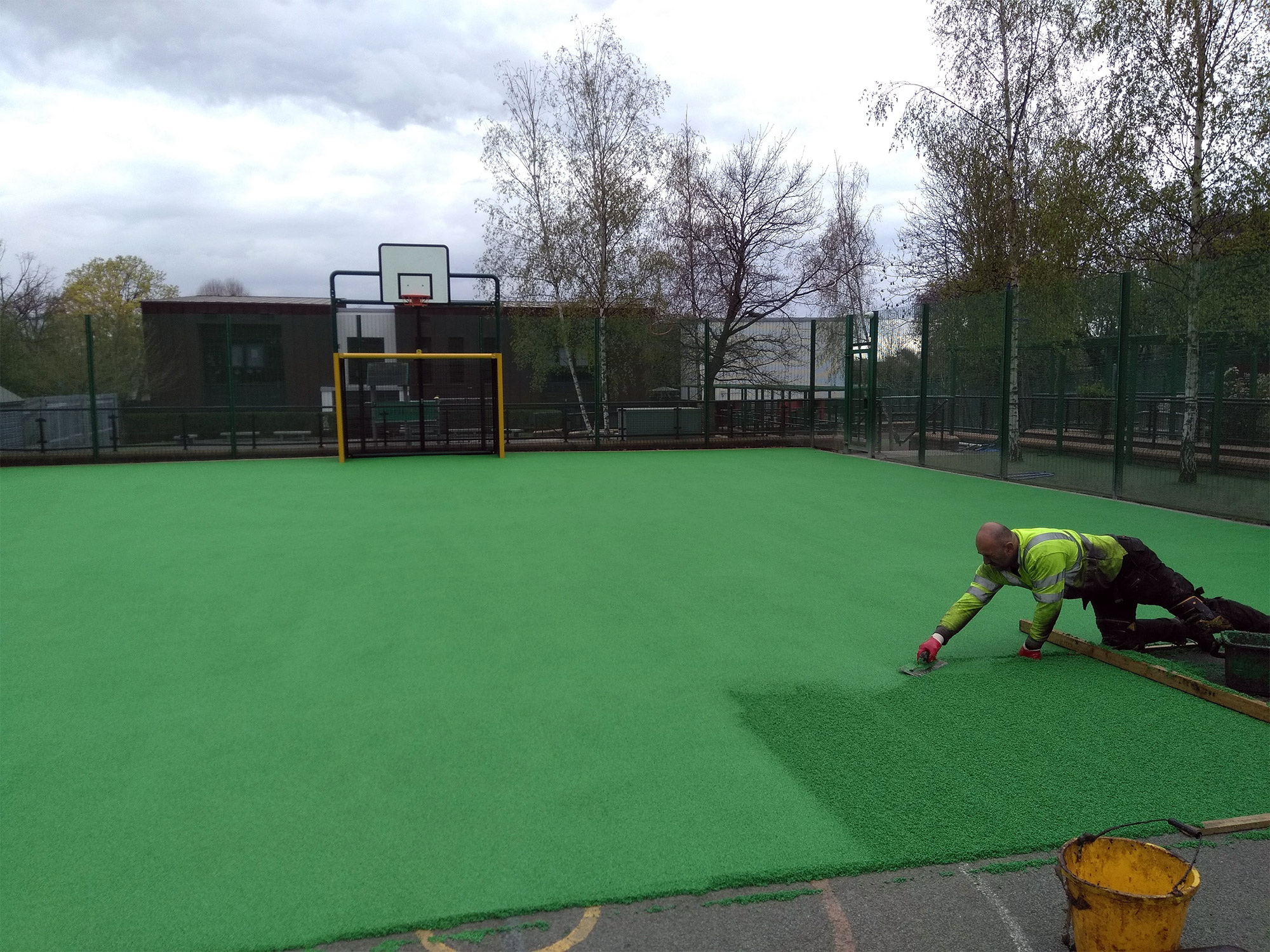
Testing
Our wet pour rubber safety surface is tested according to the requirements of BS EN1176 and BS EN1177.
A full technical specification is available on request.
Yellowing of Binder
The ‘aromatic’ binder we use in our wet pour surfaces can result in a certain degree of yellowing in the final product. This happens during the curing process, and the extent of yellowing can vary based on factors such as humidity, the angle of sunlight, and the colour selection. However, this yellowing effect is temporary and typically fades within three to six months. Importantly, this does not compromise the product’s integrity. For more information, please refer to the link titled ‘Yellowing of Binder’. The effect is most noticeable in the warmer months of the year. Yellowing of surfaces is not a defect.
Aromatic binders, which are moisture and temperature cured, cause surfaces to develop a yellowish tint. This occurrence arises due to the formation of transparent crystals during the curing process. These crystals refract light similarly to a prism, resulting in the appearance of a yellow hue when light passes through them. Notably, this yellow tint is visible upon viewing the cured surface, while the actual colour of the rubber material remains unchanged, as can be demonstrated by cross-sectional cuts.
The visibility of the yellowing effect varies based on factors such as the surface’s position, angle, and sunlight conditions. This phenomenon is particularly pronounced with colours like blue, grey, and eggshell, where yellow and blue light combine to create green. Additionally, red, and green colours tend to appear darker due to this effect, and indeed the effect with be noticeable on all colours, even black.
Blending another colour to create a fleck finish can help mitigate the visual impact of yellowing. Clients seeking extensive areas of blue, grey, or eggshell colours should be made aware of the eventual yellowing effect on the surface. While true aliphatic binders can initially minimize yellowing, they do not offer permanent protection or enhanced physical properties. Moreover, the alternative ‘aliphatic’ binders can be significantly more expensive than aromatic binders, without a guarantee that yellowing won’t occur. Therefore, Redlynch Leisure does not provide the option of using aliphatic binders.
Based on years of experience and feedback from installers, it has been observed that the yellowing phenomenon affects all moisture curing polyurethane binders, regardless of the manufacturer. However, with time, UV exposure, and surface use, the yellowing effect naturally fades away. Research indicates that this fading process typically occurs between three to six months after installation.
Get in touch today